The Science Behind Porosity: A Comprehensive Overview for Welders and Fabricators
Recognizing the complex devices behind porosity in welding is vital for welders and makers striving for impressive workmanship. From the make-up of the base products to the intricacies of the welding procedure itself, a wide variety of variables conspire to either worsen or alleviate the presence of porosity.
Recognizing Porosity in Welding
FIRST SENTENCE:
Exam of porosity in welding discloses essential insights right into the honesty and quality of the weld joint. Porosity, identified by the presence of cavities or voids within the weld metal, is an usual worry in welding processes. These gaps, otherwise correctly resolved, can endanger the structural stability and mechanical properties of the weld, causing possible failures in the finished item.

To spot and evaluate porosity, non-destructive testing approaches such as ultrasonic screening or X-ray examination are commonly used. These methods allow for the identification of inner problems without endangering the honesty of the weld. By evaluating the size, form, and circulation of porosity within a weld, welders can make informed decisions to improve their welding procedures and accomplish sounder weld joints.

Elements Affecting Porosity Formation
The occurrence of porosity in welding is influenced by a myriad of variables, varying from gas protecting performance to the intricacies of welding specification setups. Welding specifications, consisting of voltage, existing, travel speed, and electrode kind, additionally influence porosity formation. The welding technique used, such as gas metal arc welding (GMAW) or shielded steel arc welding (SMAW), can influence porosity formation due to variations in warm circulation and gas protection - What is Porosity.
Results of Porosity on Weld Top Quality
The presence of porosity likewise weakens the weld's resistance to deterioration, as the caught air or gases within the voids can react with the helpful resources surrounding setting, leading to destruction over time. In addition, porosity can prevent the weld's capacity to stand up to stress or impact, additional jeopardizing the general top quality and dependability of the bonded framework. In important applications such as aerospace, vehicle, or structural buildings, where safety and resilience are paramount, the destructive results of porosity on weld top quality can have serious repercussions, emphasizing the value of minimizing porosity through correct welding strategies and treatments.
Methods to Minimize Porosity
To boost the top quality of welded joints and ensure structural stability, welders and makers employ particular strategies targeted at lowering the development of gaps and cavities within the material during the welding process. One efficient approach to reduce porosity is to ensure appropriate product preparation. This includes comprehensive cleansing of the base steel to eliminate any type of contaminants such as oil, oil, or my latest blog post dampness that might add to porosity formation. Additionally, making use of the suitable welding parameters, such as the correct voltage, present, and travel speed, is vital in avoiding porosity. Preserving a regular arc size and angle during welding likewise helps in reducing the possibility of porosity.

Making use of the ideal welding method, such as back-stepping or employing a weaving activity, can likewise assist distribute warmth evenly and minimize the possibilities of porosity formation. By applying these methods, welders can effectively lessen porosity and generate high-grade bonded joints.
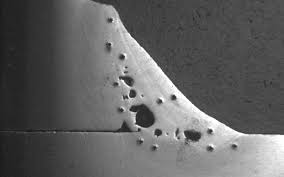
Advanced Solutions for Porosity Control
Applying innovative read this innovations and cutting-edge methods plays a pivotal function in achieving superior control over porosity in welding processes. In addition, employing innovative welding methods such as pulsed MIG welding or changed ambience welding can also help reduce porosity problems.
Another innovative option involves making use of innovative welding tools. As an example, making use of equipment with integrated functions like waveform control and innovative power sources can enhance weld quality and minimize porosity risks. In addition, the execution of automated welding systems with specific control over specifications can dramatically minimize porosity issues.
Moreover, integrating sophisticated surveillance and assessment modern technologies such as real-time X-ray imaging or automated ultrasonic screening can aid in detecting porosity early in the welding process, permitting instant rehabilitative activities. On the whole, integrating these advanced solutions can substantially enhance porosity control and boost the general high quality of bonded components.
Verdict
Finally, understanding the science behind porosity in welding is vital for welders and producers to create high-grade welds. By determining the variables affecting porosity formation and executing methods to lessen it, welders can improve the total weld top quality. Advanced options for porosity control can additionally improve the welding process and ensure a strong and reliable weld. It is essential for welders to continuously educate themselves on porosity and execute finest methods to achieve optimum outcomes.